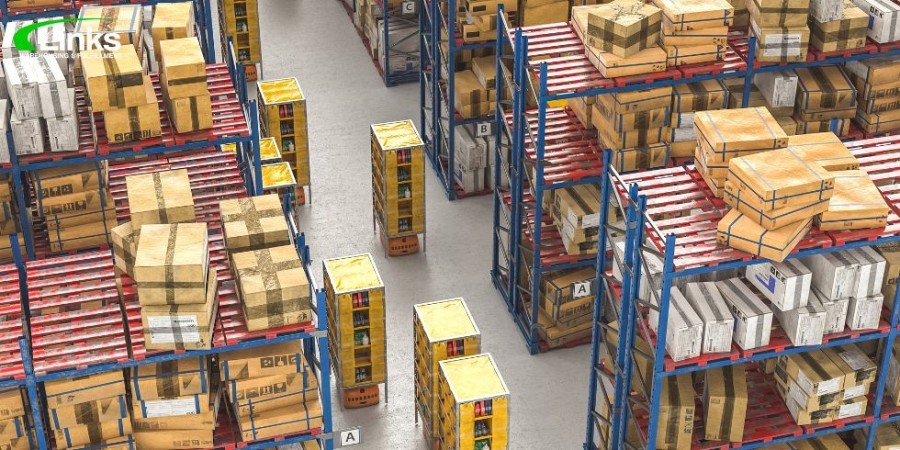
Amongst all challenges that a business, particularly e-commerce fulfillment, third-party warehousing, and other warehousing and fulfillment operations, may experience, inventory errors remain some of the costliest. The loss of stock, incorrect counting, and even minor mistakes ultimately bring huge losses and dissatisfaction among customers. An advanced WMS ensures a smooth operation and a reduction in human error. This article describes the ways an advanced WMS will contribute to the reduction of inventory errors and increase operational efficiency.
If your business is facing issues in inventory accuracy, Links Corp offers customized WMS solutions that can help your company achieve better efficiency in warehousing and fulfillment.
Common Causes of Inventory Errors
Inventory errors normally emanate from human errors, obsolete systems, and inefficient processes. For instance, manual data entry may lead to mislabeling or miscounts, which disrupt the operations of e-commerce fulfillment. Inadequate tracking in real-time causes discrepancies between the physical stock and digital records, hence presenting a challenge in third-party warehousing.
By addressing these issues, businesses can reduce costly mistakes, enhance customer satisfaction, and improve overall productivity.
Features of Advanced Warehouse Management Systems
Modern WMS technologies come equipped with powerful features to combat inventory errors. These systems integrate real-time tracking through IoT and RFID technology, ensuring businesses always know their inventory levels. Automated data capture, such as barcode scanning, eliminates manual entry mistakes.
Furthermore, the more evolved WMS solutions automatically synchronize with ERP and CRM systems to make sure all business platforms have updates in real-time. This is very helpful for warehousing and fulfillment providers who deal with inventory meant for different clients. Predictive analytics further help in the attainment of efficiency by detecting potential discrepancies before they can escalate.
For businesses, these features are game changers that enable them to meet client demands without error-related disruptions.
How WMS Reduces Inventory Errors
- Correct Stock Counts: Automation minimizes discrepancies in the stock-taking processes. This is quite important for companies handling e-commerce fulfillment where inventory turnover is very rapid.
- Smoother Operations: Besides minimizing errors, the elimination of manual processes also speeds up the pace of workflows. Companies using WMS in their warehousing and fulfillment operations claim to save a lot of time and money.
- Improved Visibility: Access to real-time data enhances collaboration between teams and prevents errors before they happen. This is very important in third-party warehousing, where inventory is in constant motion.
- Anomaly Detection: Advanced WMS systems have anomaly detection capabilities that flag issues for immediate correction.
For e-commerce businesses seeking the best optimization of their fulfillment and warehousing and fulfillment operations, Links Corp offers industry-leading WMS solutions tailored to your needs.
Overcoming WMS Implementation Challenges
While there are some initial costs and training associated with implementing a WMS, a WMS is worth the investment. The challenges can be mitigated if the business selects a scalable system and partners with providers, such as Links Corp, that provide complete support throughout implementation.
Take Your Business to the Next Level with Links Corp
Inventory accuracy is of utmost importance for e-commerce fulfillment, third-party warehousing, and warehousing and fulfillment companies. Advanced warehouse management systems reduce errors, increase efficiency, and result in significantly improved customer satisfaction. If your business is ready to take its inventory management to the next level, contact Links Corp today to explore customized WMS solutions.